From Design to Installation – Bespoke School Furniture
Witley Jones has proudly designed, manufactured and installed school furniture for over 20 years; we understand the unique demands within the education environment and across school estates.
We thought that by sharing an insight into our manufacturing process, from design to installation, it would demonstrate the high level of care we take and why school’s choose us?
Here is an insight into the journey that involves…
Design
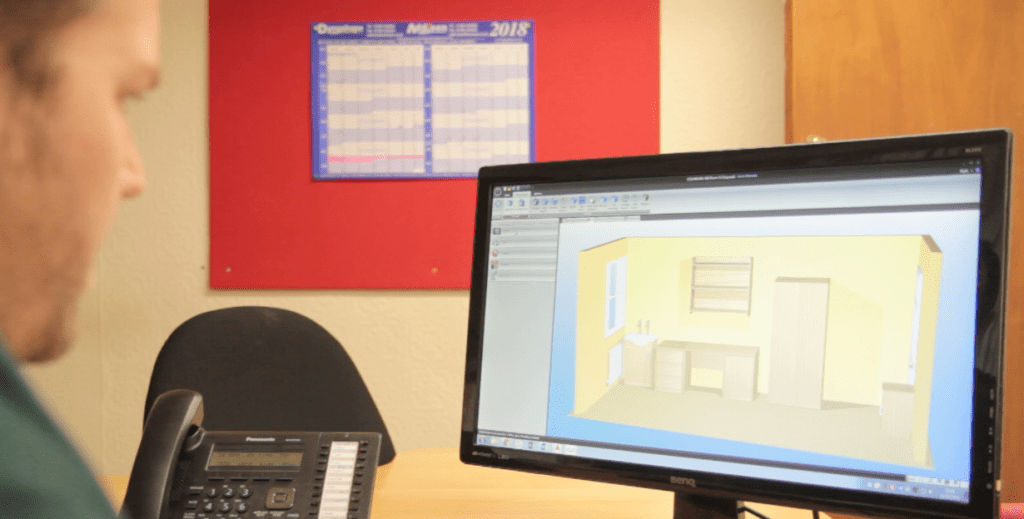
After initial contact, we always try to come and meet our customers wherever possible. We feel that by seeing you in person and visiting your school, we can gain a much greater understanding of the environment and people we are working with and how you imagine it looking; from here we build a design brief.
We undertake a survey to allow our drawing office to provide 2D and 3D visuals, establishing finishes, layouts and numbers. If we are working with a building contractor, we request floor plans which allow us to begin drawing. The drawings can be amended as projects develop to ensure the end user has the best experience.
Once the detail is established we begin pricing and, together with the drawings, the quotation forms the initial proposal for your consideration. Quite often we give different room layout options or different levels of delivery and/or installation to allow you to choose the package that best suits you.
Manufacturing
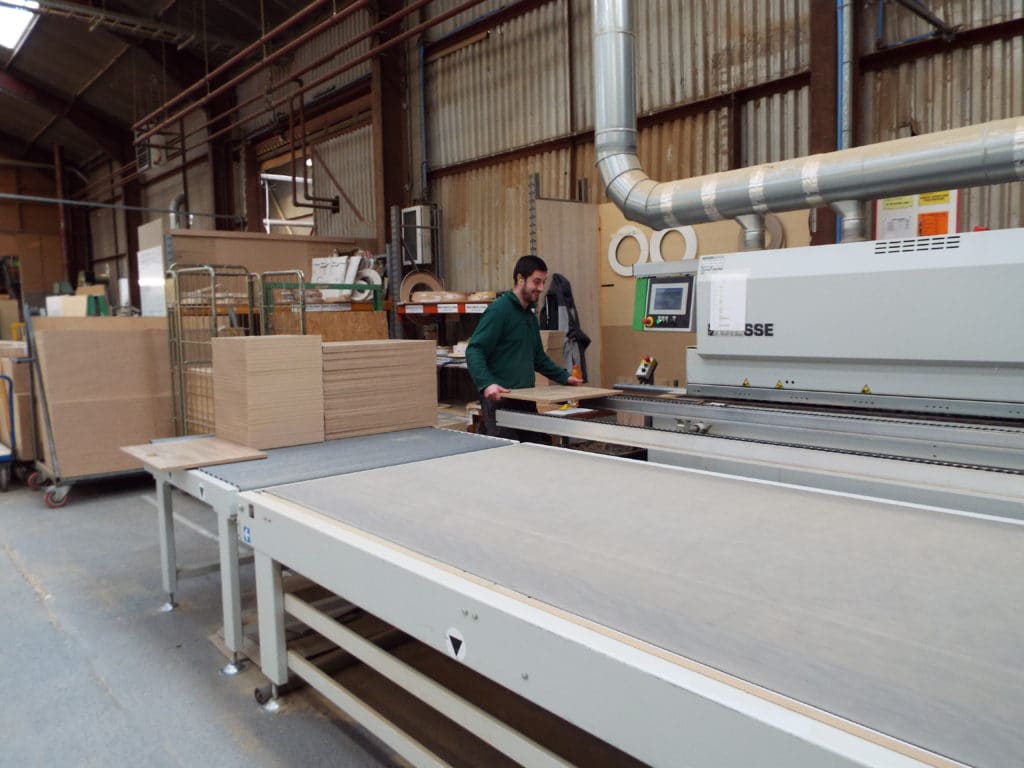
Our orders are ‘optimised’ and paperwork is written to ensure a smooth transition from computer screen through to dispatch. The specification is translated into Project Checklists, which are issued to the factory for our assembly team to begin the building process.
Starting in the machine shop and finishing in our brand new assembly factory, this process takes in CNC machinery, edge banding, sanding and spray shops, assembly benches, wrapping and labelling. Whether it be a naturally veneered finish using formaldehyde free lacquer or a melamine faced finish using our robust cam and dowel hardware, the same level of care is afforded to each item of furniture.
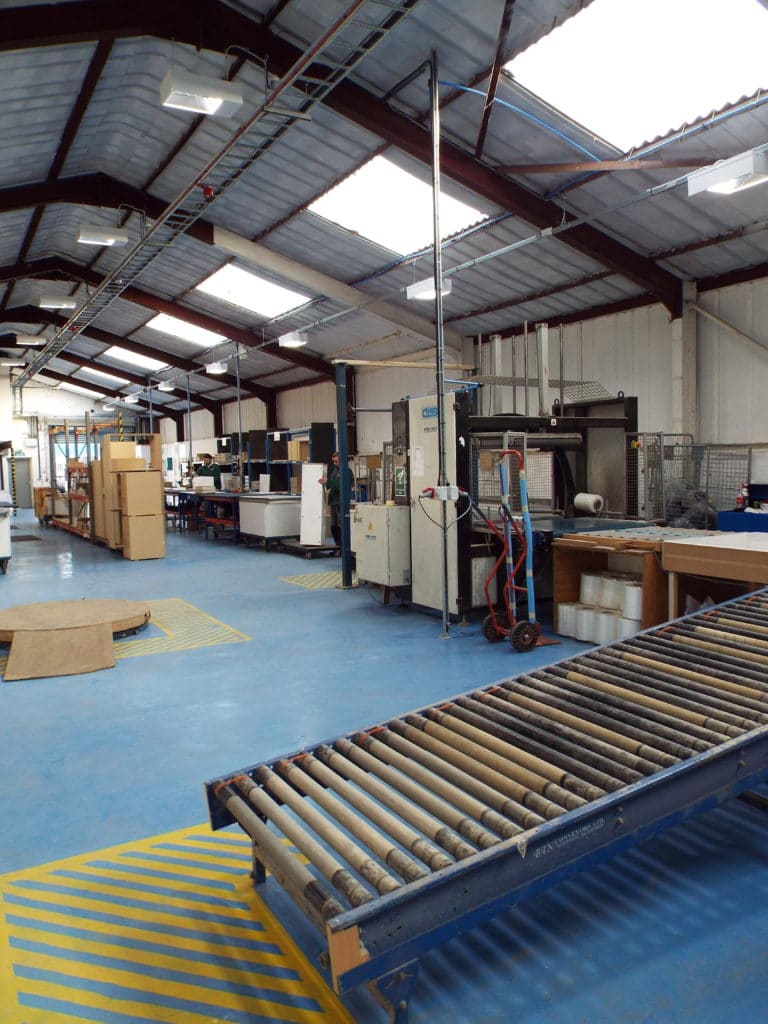
Our multi-skilled and flexible workforce work to ensure your furniture is exactly how you imagined. Our drawing and manufacturing software works in tandem to ensure a smooth transition from our drawing office to your doorstep.
Installation
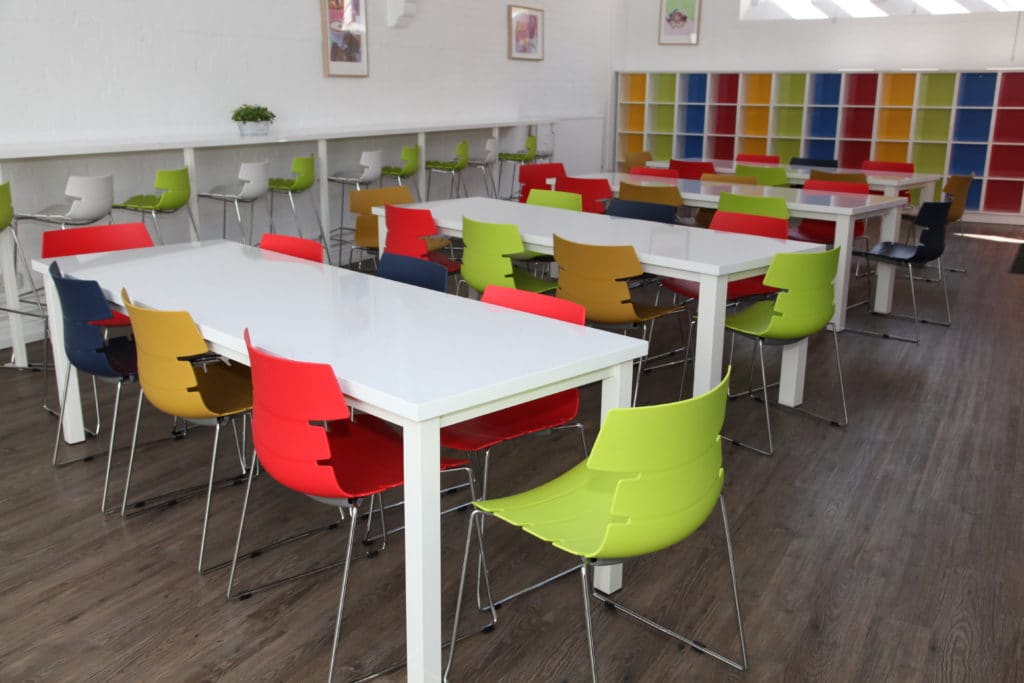
You may or may not have the resources to carry in and install your furniture yourselves. We have highly skilled installation teams who travel the country fitting furniture. Whether it be a driver only kerbside delivery of mattresses, or a brand new building contractor-occupied boarding house, we can tailor the delivery and installation to suit you.
All of our fitters have enhanced DBS certificates and we are CHAS and ConstructionLine accredited. Our fitting teams hold CSCS cards too, allowing us to work on live building sites and under the time constraints that many of these projects can involve. Witley Jones are well versed in this and pride ourselves on the level and quality of service we offer all of our customers.
Our fitters leave rooms clean and ready for use and will always seek your approval and sign-off before leaving. They then complete one final check to ensure everything is in perfect working condition before leaving you to enjoy your new furniture.
Stay up to date with furniture design trends
Subscribe to our newsletter and follow us on Twitter or LinkedIn.